Energy Savings Using VFD's
- Apr 6, 2020
- 3 min read
Dustin Olson - Product Specialist
December 2018
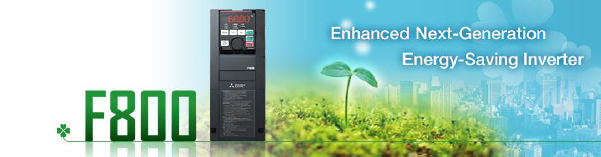
What is a VFD? A variable frequency drive, also known as a VFD or Inverter, is a superior way of powering an AC induction motor when compared to powering directly across the line or with a soft starter. Some of the benefits gained by using a VFD include; smooth acceleration and deceleration, limited inrush current, higher motor efficiency, and operation at any frequency in the range of 0- 400Hz.
What are VFD’s used for? VFD’s are used to control the speed, torque and position of a motor shaft. They also provide many features to protect and prolong the life of your motor. VFDs are typically used for Fan, Pumping and Conveyor applications but can be used with any inverter rated AC Induction motor.
How can a VFD save energy? Motors applied to fans and pumps are typically oversized. Up to a 20% oversize is common due to NEMA motor power frame sizes and general engineering practice to add a small overhead. This 20% oversize provides an opportunity for users to save energy when applying a VFD. The VFD will allow you to run your motor at a speed that the application requires, that being less flow, slower speed, resulting in significant energy savings. The superior control of a VFD allows you to cut any unnecessary acceleration, decelerations and speed out of the motor’s motion which will save energy and reduce mechanical stress. For example in fan applications that use a mechanical dampener to restrict air flow. The damper can be opened fully and the speed of the motor can be slowed to reduce airflow, which will save energy instead of restricting the flow with a dampener and running the fan at full speed.

Example Application with Return on Investment Calculated with and without a VFD for energy savings.
Situation: A 50hp Ventilation Fan running all day, every day, with an Outlet Damper that is active 20% of the time. Cost per kWh: $0.1 Motor Size: 50hp (37.285 kW) Motor Runtime: 24 hours a day X 365 days a year (8760 hours a year)
Energy Costs Without an Energy Saving VFD:
Runtime Hours X Motor’s Kilowatt Rating = Kilowatts/hr over the full year 8,760 Runtime Hours X 37.285 KW = 326,616.6 kWh
Kilowatts/hr over the full year X Cost Per Kilowatt Hour = Energy cost per year 326,616 kWh X $0.1 per kWh = $32,661.60 Energy cost per year.
$32,661.60 per year in energy costs
Addition of a VFD: Inverter: FR-F820-01540-E360 Inverter Cost: $4,889.00 Excel Energy Rebate: -$3,500.00 Inverter net cost: $1,389.00
The Required Flow is 80%, instead of closing the dampener, we can shut off the motor and save energy. 8,760 X 80% = 7,008 running hours
Systems are typically oversized by up to 20%. NEMA motor frame sizes and engineering practice. This is often not corrected after an application is installed.
60Hz X 80% = 48Hz 48Hz/60Hz = .8 .83 X 37.285 = 19.08 kW motor rating
Energy Costs With an Energy Saving VFD:
Runtime Hours X Motor’s Kilowatt rating = Kilowatts/hr over the full year. 7,008 X 19.08 = 133,712.64 kWh Kilowatts/hr over the full year X Cost Per Kilowatt hour = Energy cost per year 133,712.64 kWh X $0.1 = $13,371.26
$13,371.26 per year in energy costs
Energy Savings:
Without a VFD Annual Cost – With a VFD annual cost = savings per year $32,661.66 – $13,371.26 = $19,290.40 savings per year.
Return on Investment (ROI):
Savings per year / number of days in year = amount saved per day $19,290.40 / 365 days = $52.85 saved a day Installation cost /Amount saved per day = days to recover initial investment $1,389 / $52.85 = 26.28 days 26.28 days until initial investment is recovered
Additional Resources
Download Mitsubishi Energy Saving ROI Software:
Additional Application Examples from Mitsubishi Electric:
コメント